නිරවද්ය ලෝහ කොටස් බොහෝ විට විවිධ නිරවද්ය යන්ත්රෝපකරණ තාක්ෂණයන් භාවිතයෙන් නිෂ්පාදනය කරනු ලබන අතර, CNC යන්ත්රෝපකරණ පොදු ක්රමයකි. සාමාන්යයෙන්, නිරවද්ය කොටස් සාමාන්යයෙන් මානයන් සහ පෙනුම යන දෙකටම ඉහළ ප්රමිතීන් ඉල්ලා සිටී.
එබැවින්, ඇලුමිනියම් සහ තඹ වැනි CNC යන්ත්රෝපකරණ ලෝහ භාවිතා කරන විට, නිමි භාණ්ඩයේ මතුපිට මෙවලම් සලකුණු සහ රේඛා ඇතිවීම කනස්සල්ලට කරුණකි. ලෝහ නිෂ්පාදන යන්ත්රෝපකරණ අතරතුර මෙවලම් සලකුණු සහ රේඛා ඇතිවීමට හේතු මෙම ලිපියෙන් සාකච්ඡා කෙරේ. විභව විසඳුම් ද අපි යෝජනා කරමු.
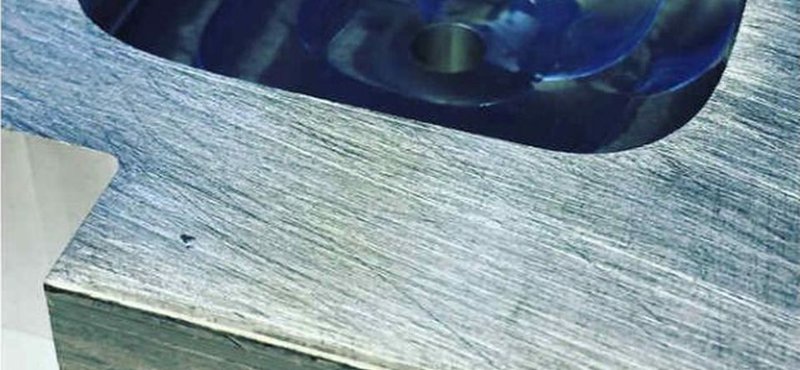
සවිකිරීම්වල කලම්ප බලය ප්රමාණවත් නොවීම
හේතු:සමහර කුහර ලෝහ නිෂ්පාදන සඳහා රික්ත සවිකිරීම් භාවිතා කිරීමට අවශ්ය වන අතර, මතුපිට අක්රමිකතා පැවතීම හේතුවෙන් ප්රමාණවත් චූෂණ ජනනය කිරීමට අරගල කළ හැකි අතර, එහි ප්රතිඵලයක් ලෙස මෙවලම් සලකුණු හෝ රේඛා ඇති වේ.
විසඳුමක්:මෙය අවම කිරීම සඳහා, පීඩනය හෝ පාර්ශ්වීය ආධාරක සමඟ ඒකාබද්ධව සරල රික්ත චූෂණ සිට රික්ත චූෂණ දක්වා මාරුවීම සලකා බලන්න. විකල්පයක් ලෙස, නිශ්චිත කොටස් ව්යුහයන් මත පදනම්ව විකල්ප සවිකිරීම් විකල්ප ගවේෂණය කරන්න, විශේෂිත ගැටලුවට විසඳුම සකස් කරන්න.
ක්රියාවලි ආශ්රිත සාධක
හේතු:ඇතැම් නිෂ්පාදන නිෂ්පාදන ක්රියාවලීන් මෙම ගැටලුවට දායක විය හැකිය. නිදසුනක් ලෙස, ටැබ්ලට් පරිගණක පසුපස කවච වැනි නිෂ්පාදන, පැති සිදුරු සිදුරු කිරීම සහ දාර CNC ඇඹරීම ඇතුළත් යන්ත්රෝපකරණ පියවර අනුපිළිවෙලකට භාජනය වේ. ඇඹරීම පැති සිදුරු ස්ථාන කරා ළඟා වන විට මෙම අනුපිළිවෙල සැලකිය යුතු මෙවලම් සලකුණු වලට හේතු විය හැක.
විසඳුමක්:ඉලෙක්ට්රොනික නිෂ්පාදන කවච සඳහා ඇලුමිනියම් මිශ්ර ලෝහය තෝරා ගැනීමේදී මෙම ගැටලුවේ පොදු අවස්ථාවක් සිදු වේ. එය විසඳීම සඳහා, පැති සිදුරු සිදුරු කිරීම සහ ඇඹරීම වෙනුවට CNC ඇඹරීම පමණක් භාවිතා කිරීමෙන් ක්රියාවලිය වෙනස් කළ හැකිය. ඒ සමඟම, ස්ථාවර මෙවලම් සම්බන්ධතාවය සහතික කිරීම සහ ඇඹරීමේදී අසමාන කැපීම අඩු කිරීම.
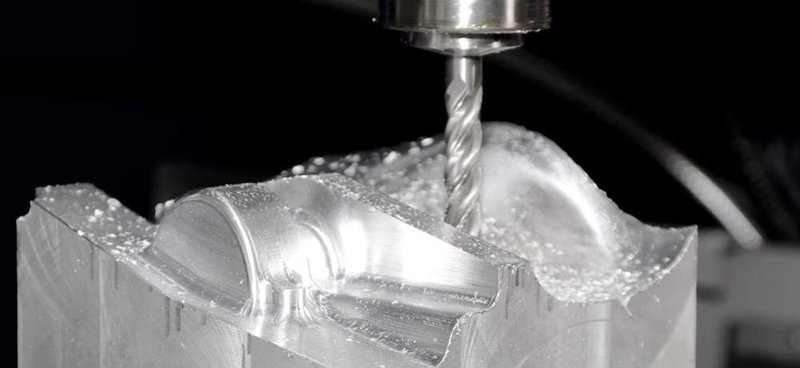
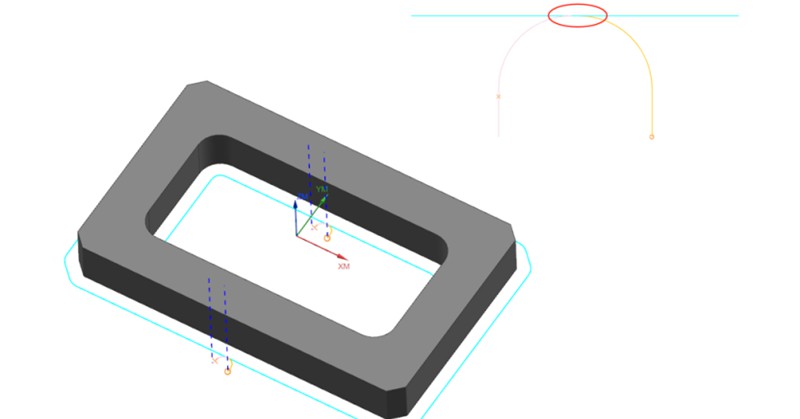
මෙවලම් මාර්ග සම්බන්ධතාවය ප්රමාණවත් නොවන ක්රමලේඛනය
හේතු:මෙම ගැටළුව සාමාන්යයෙන් නිෂ්පාදන නිෂ්පාදනයේ 2D සමෝච්ඡ යන්ත්රෝපකරණ අවධියේදී පැන නගී. CNC වැඩසටහනේ දුර්වල ලෙස නිර්මාණය කරන ලද මෙවලම් මාර්ග සම්බන්ධතාවය, මෙවලමෙහි ඇතුල්වීමේ සහ පිටවීමේ ස්ථානවල සලකුණු තබයි.
විසඳුමක්:ඇතුල්වීමේ සහ පිටවීමේ ස්ථානවල මෙවලම් සලකුණු වළක්වා ගැනීමේ අභියෝගයට මුහුණ දීම සඳහා, සාමාන්ය ප්රවේශයක් වන්නේ මෙවලම් සම්බන්ධ කිරීමේ දුරෙහි (ආසන්න වශයෙන් 0.2mm) සුළු අතිච්ඡාදනයක් හඳුන්වා දීමයි. මෙම තාක්ෂණය යන්ත්රයේ ඊයම් ඉස්කුරුප්පු නිරවද්යතාවයේ ඇති විය හැකි සාවද්යතාවයන් මඟ හැරීමට සේවය කරයි.
මෙම උපාය මාර්ගය මෙවලම් සලකුණු සෑදීම ඵලදායී ලෙස වළක්වන අතර, නිෂ්පාදනයේ ද්රව්යය මෘදු ලෝහයක් වන විට එය පුනරාවර්තන යන්ත්රෝපකරණ මූලද්රව්යයක් ඇති කරයි. එහි ප්රතිඵලයක් ලෙස, මෙම කොටස අනෙකුත් ප්රදේශ හා සසඳන විට වයනය සහ වර්ණයෙහි වෙනස්කම් පෙන්නුම් කළ හැකිය.
පැතලි යන්ත්රගත මතුපිට මත මාළු කොරපොතු රටා
හේතු:නිෂ්පාදනයේ පැතලි පෘෂ්ඨ මත දිස්වන මාළු කොරපොතු හෝ රවුම් රටා. ඇලුමිනියම්/තඹ වැනි මෘදු ලෝහ සැකසීම සඳහා භාවිතා කරන කැපුම් මෙවලම් සාමාන්යයෙන් නළා 3 සිට 4 දක්වා මිශ්ර ලෝහ ද්රව්ය මෝල් වේ. ඒවාට HRC55 සිට HRC65 දක්වා පරාසයක දෘඪතාවක් ඇත. මෙම ඇඹරුම් කැපුම් මෙවලම් මෙවලමෙහි පහළ දාරය භාවිතයෙන් සිදු කරනු ලබන අතර, කොටසේ මතුපිට එහි සමස්ත පෙනුමට බලපාන සුවිශේෂී මාළු කොරපොතු රටා වර්ධනය විය හැකිය.
විසඳුමක්:ඉහළ පැතලි බව අවශ්යතා සහ අවපාත ව්යුහයන් සහිත පැතලි මතුපිටක් සහිත නිෂ්පාදනවල බහුලව දක්නට ලැබේ. මෙයට පිළියමක් වන්නේ සුමට මතුපිට නිමාවක් ලබා ගැනීමට උපකාරී වන කෘතිම දියමන්ති ද්රව්ය වලින් සාදන ලද කැපුම් මෙවලම් වෙත මාරු වීමයි.
උපකරණ සංරචක වයසට යාම සහ ගෙවී යාම
හේතු:නිෂ්පාදන මතුපිට ඇති මෙවලම් සලකුණ උපකරණයේ ස්පින්ඩලය, ෙබයාරිං සහ ඊයම් ඉස්කුරුප්පු වල වයසට යාම සහ ගෙවී යාම නිසා ඇතිවේ. මීට අමතරව, ප්රමාණවත් නොවන CNC පද්ධති පසුබෑමේ පරාමිතීන්, විශේෂයෙන් වටකුරු කොන් යන්ත්රෝපකරණ කිරීමේදී උච්චාරණ මෙවලම් සලකුණු වලට දායක වේ.
විසඳුමක්:මෙම ගැටළු උපකරණ ආශ්රිත සාධක වලින් පැන නගින අතර ඉලක්කගත නඩත්තුව සහ ප්රතිස්ථාපනය මගින් විසඳා ගත හැකිය.
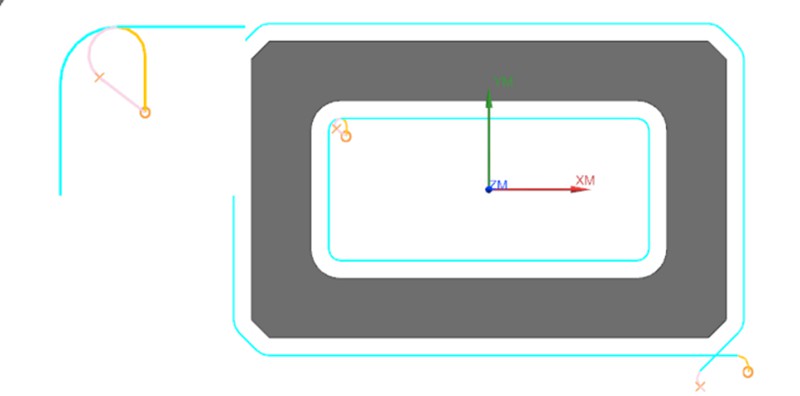
නිගමනය
CNC යන්ත්රෝපකරණ ලෝහවල පරමාදර්ශී මතුපිටක් ලබා ගැනීම සඳහා ප්රයෝජනවත් ප්රවේශයන් අවශ්ය වේ. උපකරණ නඩත්තු කිරීම, සවිකිරීම් වැඩිදියුණු කිරීම්, ක්රියාවලි ගැලපීම් සහ ක්රමලේඛන පිරිපහදු කිරීම් වල එකතුවක් ඇතුළත් මෙවලම් සලකුණු සහ රේඛා වළක්වා ගැනීමට විවිධ ක්රම තිබේ. මෙම සාධක තේරුම් ගෙන නිවැරදි කිරීමෙන්, නිෂ්පාදකයින්ට නිරවද්ය සංරචක මාන නිර්ණායක සපුරාලීම පමණක් නොව අපේක්ෂිත සෞන්දර්යාත්මක ගුණාංග ද ප්රදර්ශනය කරන බව සහතික කළ හැකිය.